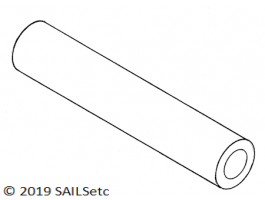
Aluminothermy Welding: How To Execute It Properly
In aluminothermy welding, a host of factors influence the quality of the weld. The weld is performed by an operator. The manual welding work is not very consistent but the preparation and the execution are well and truly described in detail. Operators receive training with instructions and steps to follow. If these are followed correctly, you get a good quality weld. The rail deburring device happens to be the best here.
Preparation
For a weld, two parts of rails must be joined together. Most often it is an old part and a new replacement part. These are sawn and juxtaposed. The new part is welded to an old rail. Both rails are slightly raised to get a better fit. So you have more mass in the head than in the foot. When the weld cools, the rail goes down a little, so that the rail is properly horizontal.
The templates used for aluminothermy welding are made of ceramic material with the shape of the rail in it. These are placed on the rail and must be well aligned. The space between the template and the rail is filled with sand or some sort of paste for sealing. When the template is in place, preheating can begin. In aluminothermy welding, this heating is done by an external source, namely propane. The steel must be heated to about 700 ° C. Since it is difficult to measure the temperature, we work with waiting times. After about 5 minutes, the steel has reached the correct temperature.
Execution
After preheating, the crucible with the thermite charge is deposited on the template. Thermite is not considered a hazardous product because it is not flammable in principle. You need a very high temperature to initiate it. This is still done temporarily with a magnesium bar but more and more electric ignition of the aluminothermic reaction is being considered. The reason is that it requires a special permit for the transportation of magnesium bars.
Due to the high temperatures in the melting pot some 3,000 ° C about 11 kilograms of molten steel are formed. It flows in the template, reaches the foot along the sides and goes up as well. The most used process here is that the steel goes up along the foot.
When all the steel has passed, certain durations must be taken into account.
Above all, the time required to cut excess material with a hydraulic shear. This cannot be done too early because you still have liquid steel but you cannot wait too long either. When this is fully solidified, you do not cross it anymore.
Control and life
It’s hard to know if the weld is good or not. This is why we control in two ways, namely visual inspection and geometrical inspection. In particular, the presence of tears or porosity is considered, if everything is clean and the alignment and height are correct.
The life of the weld is normally as long as the life of a train rail. On average 25 years, but this also depends on the frequency of use of the rail lines where the rails are.
Conclusion
Aluminothermy welding is a widely used method of welding rails together. It seems simple to follow all the steps but many problems can arise. But if everything goes well during the welding, you have a qualitative weld that is able to last for many years.